Threading and Deburring in one operation
Thread Mills from SmiCut (ThreadBurr) will give you a nice entry and a burr free thread.
- Threading and Deburring in one operation
- No additional time for deburring
The deburring operation is made automatically when thread milling, which gives you the deburring without any extra costs. There is no disadvantage to use the ThreadBurr, even if you don´t use the deburring function. ThreadBurr is standard on all thread mills from SmiCut.
Vibration-Free Thread Mills
Many of these Thread Mills have a unique vibration-free design, resulting in improved productivity. Discover the advantages of this innovative feature by clicking here.
Click here if you have trouble watching the video
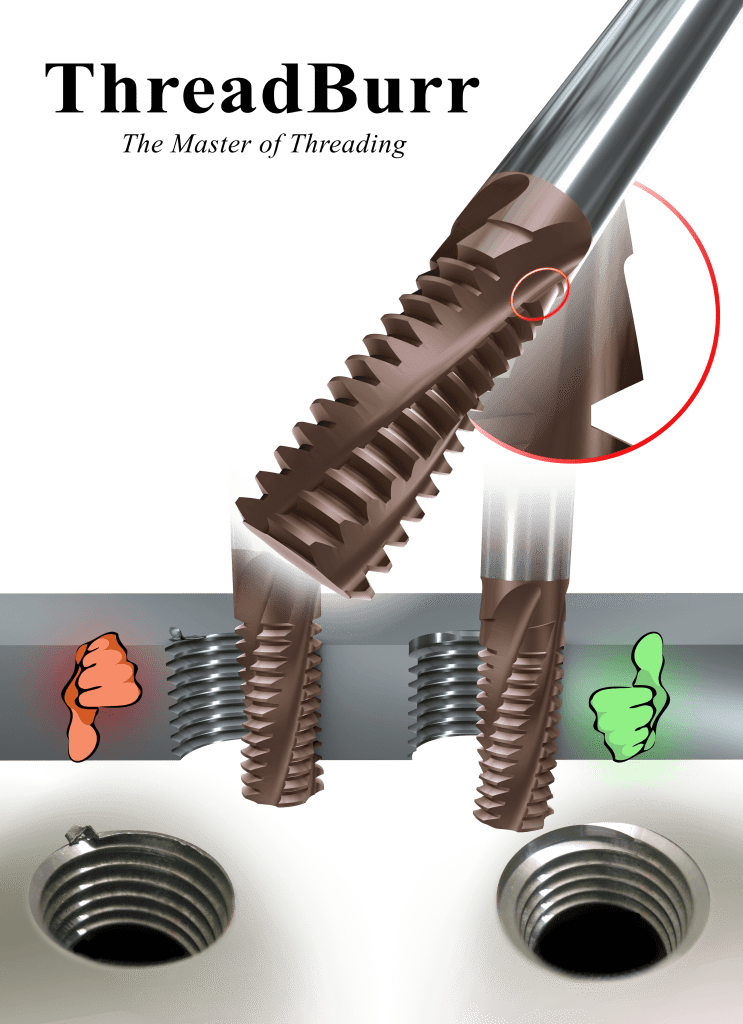
With Solid Carbide Thread Mills from SmiCut you can thread and deburr in one operation.
How to get a burr free Thread
The cutting length is laser marked on the tool and you can find it as well in the catalogue. This is the distance you should go in to the hole from the surface to get a perfect entry.
Watch part 3 of the SmiProg video series for more information of how to use ThreadBurr.
Throught holes
You can always use a standard tool for through holes. Please take in mind you should use a tool as short as possible to get best stability and economy.
Blind Holes
With blind holes it is important to have the correct cutting length (l) on the tool to get the thread deburred. Normally you will find a suitable standard tool. If not, we will cut the tool to the correct length with extremely short delivery time and at a reasonable price. Have in mind the following when you order a tool for blind holes.
- The cutting length (l) should be required thread length (L) plus one pitch (P).
- The distance to cut off (c) has to be dividable by the pitch (P).
Example
M16x1,5 thread length 24 mm
Thread Milling with NB1212D29_1.5ISO_AC (L = 29,25 mm)
24 + 1,5 = 25,5 mm | Required cutting length (l) |
29,25 -25,5 = 3,75 mm | Maximum cutting off |
3,75 / 1,5 = 2,5 | Number of pitches to cut off |
2 x 1,5 = 3,0 mm | Distance to cut off (c) |
29,25 – 3,0 = 26,25 mm | Cutting length (l) after cutting off |
26,25 – 1,5 = 24,75 mm | Thread length (L) after cutting off |
You only need to cut of the tool when you want to use the deburring function on blind holes and if there is no standard tool with suitable cutting length.
Get the thread deburred on both sides with Double ThreadBurr
It is possible to get the thread deburred on both sides. For this operation you need to use a special tool as thread length depends on the thickness of the material. Read a case study report about Double ThreadBurr. Have in mind the following when you order a tool for deburring on both sides.
- The cutting length (l) should be equivalent to the thickness of the material.
Example
M30x3 thread lenth 40 mm
40 / 3 = 13,3 | Number of pitches |
13 x 3 = 39,0 mm | Cutting length (l) |
Thread Milling with custom made tool NBB2020D39_3.0ISO_AC (l = 39,0 mm)